Selecting the best for tank cleaning
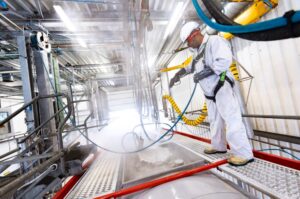
How critical are tank cleaning stations to your logistics operations, and what impact do they have on efficiency and compliance?
This is very critical, as cleaning our tank containers will help us avoid certain risks and protect our reputation and liability.
Tank cleaning is not only a matter of safety and compliance, but it is also about efficiency and productivity.
A clean tank can perform better, last longer and save us money in the long run. Tanks that are not cleaned frequently and/or properly can accumulate sludge, sediment, scale, rust and other residues that can reduce their functionality and contaminate products.
What are the key factors you consider when selecting a tank cleaning station — location, facilities, cost, or compliance standards?
First of all we only select cleaning stations, which have dedicated foodstuff cleaning bays.
A second step in our process is to perform an evaluation of the SQAS-cleaning report. This SQAS report is issued by an independent SQAS assessor and outlines both technical and organisational facts and figures, which allow us to get a good picture of the performance of the cleaning station.
Other key factors might be that our customers have a specific and audited cleaning station to use, which we then adapt.
How do regulations and industry standards influence your choice of tank cleaning stations, particularly concerning safety and environmental concerns?
As described above, our selection and approval process in using a cleaning station is linked to their ability to offer dedicated foodstuff cleaning bays and their SQAS score.
What challenges have you faced with tank cleaning stations in the past, and how do you mitigate risks such as contamination or delays?
There are no challenges that we are facing thus far, especially because of the selection and approval process applied by us.
To what extent does the availability of additional services (e.g., heating, drying, or waste disposal) affect your decision when choosing a cleaning station?
These elements are nice to have, as we are seeking a one-stop shop to purchase the services we need.
However, this is certainly not the most important factor in our cleaning decision process as first, and utmost, we seek the guarantee that our foodstuff ISO tanks are being cleaned as per our set requirements and industry standards.
How important is digitalisation or real-time tracking of cleaning processes in your selection of a tank cleaning station and does it impact your operational planning?
We strive for quick turnaround times at the cleaning stations and depots we use as we want to deliver to our clients with their high demands. Real time communication is key to this, so we expect our cleaning stations to provide this communication swiftly.
Additionally, cotac is an integral part of the full-service portfolio of the Hoyer Group.
Worldwide, 12 locations at logistics hubs in Europe, Asia and the US support the logistics processes and products of Hoyer in close partnership.
cotac ensures globally uniform standards for tank cleaning, repair and depot services and is regularly audited in accordance with DIN EN-ISO 9001 and SQAS.
The technical services provided by cotac ensure the smooth, efficient and safe transport logistics of the HOYER Group – and it does so all over the world.
For more information: hoyer-group.com
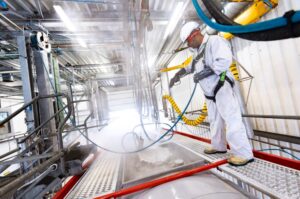